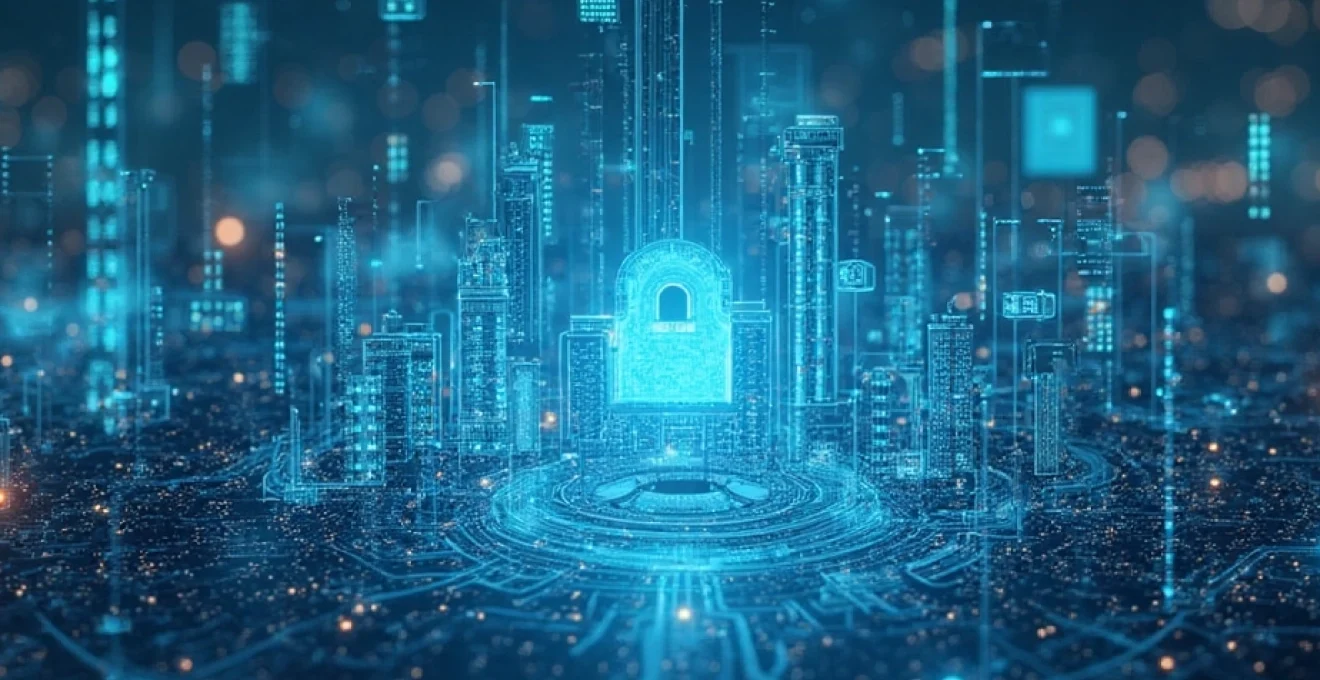
In today’s rapidly evolving industrial landscape, organizations are constantly seeking ways to optimize their operations, boost productivity, and stay ahead of the competition. The integration of smart technologies, robust security measures, and customized solutions has become paramount in achieving these goals. By leveraging cutting-edge automation, data analytics, and connectivity, industries can transform their processes and unlock new levels of efficiency and innovation.
As we delve into the world of industrial optimization, it’s crucial to understand how these advanced technologies are reshaping manufacturing, supply chain management, and overall business operations. From the factory floor to the boardroom, the impact of these smart solutions is felt across every aspect of industrial enterprises.
Optimizing production processes through automation technology
Automation technology has revolutionized the way industries approach production. By implementing sophisticated systems and machinery, companies can significantly enhance their output quality, reduce errors, and minimize downtime. The key to successful automation lies in selecting the right technologies and integrating them seamlessly into existing workflows.
Robotics integration for precision manufacturing tasks
Robotics has become an integral part of modern manufacturing, offering unparalleled precision and consistency in various tasks. From assembly lines to quality control, robots are capable of performing repetitive actions with a level of accuracy that surpasses human capabilities. This integration not only improves product quality but also allows human workers to focus on more complex, value-added activities.
For instance, in the automotive industry, robotic arms equipped with advanced sensors can perform welding tasks with micron-level precision, ensuring the structural integrity of vehicles while maintaining high production rates. The use of collaborative robots, or cobots, has also gained traction, allowing for safe human-robot interaction in shared workspaces.
Machine learning algorithms enabling predictive maintenance
One of the most significant advancements in industrial efficiency is the application of machine learning algorithms for predictive maintenance. By analyzing vast amounts of data collected from sensors and equipment, these algorithms can predict when machinery is likely to fail, allowing for proactive maintenance scheduling.
This approach significantly reduces unplanned downtime, which can cost industries millions in lost productivity. For example, a paper mill implementing predictive maintenance techniques reported a 50% reduction in unexpected breakdowns within the first year of implementation. The ability to foresee and prevent equipment failures not only saves money but also extends the lifespan of machinery.
Real-time data analysis driving process improvements
The power of real-time data analysis cannot be overstated in the context of industrial optimization. By leveraging advanced analytics platforms, companies can gain instant insights into their operations, identify bottlenecks, and make data-driven decisions to improve efficiency.
Real-time monitoring allows for immediate adjustments to production parameters, ensuring optimal performance and resource utilization. For instance, a chemical processing plant using real-time analytics was able to reduce energy consumption by 15% by fine-tuning its processes based on live data feeds. This level of responsiveness is crucial in today’s fast-paced industrial environment.
Enhancing supply chain visibility via IoT connectivity
The Internet of Things (IoT) has transformed supply chain management by providing unprecedented visibility into every stage of the production and distribution process. Connected devices and sensors create a network of information that allows for real-time tracking, inventory management, and demand forecasting.
By implementing IoT solutions, companies can achieve a level of transparency that was previously unattainable. This enhanced visibility leads to more efficient inventory management, reduced waste, and improved customer satisfaction. For example, a large retailer implementing IoT-based supply chain management reported a 30% reduction in out-of-stock incidents and a 25% decrease in inventory holding costs.
The integration of IoT also facilitates better coordination between different parts of the supply chain. Suppliers, manufacturers, and distributors can share real-time information, allowing for more accurate planning and faster response to market changes. This level of connectivity is essential in creating a resilient and agile supply chain capable of adapting to disruptions and fluctuating demand.
Ensuring robust cybersecurity across industrial control systems
As industries become increasingly digitized, the importance of robust cybersecurity measures cannot be overstated. Industrial control systems (ICS) are particularly vulnerable to cyber threats, and a breach can have severe consequences, including production halts, data loss, and even physical damage to equipment.
Multi-layered defense strategies protecting critical infrastructure
To safeguard against cyber threats, industries must adopt a multi-layered approach to security. This strategy involves implementing various security measures at different levels of the industrial network, creating a comprehensive defense system. Key components of a multi-layered defense include:
- Network segmentation to isolate critical systems
- Strong authentication protocols and access controls
- Encryption of sensitive data both at rest and in transit
- Regular security audits and vulnerability assessments
- Intrusion detection and prevention systems
By implementing these layers of protection, industries can significantly reduce the risk of successful cyber attacks and protect their critical infrastructure from potential threats.
Continuous threat monitoring mitigating operational risks
In the ever-evolving landscape of cyber threats, continuous monitoring is essential for maintaining a strong security posture. Advanced threat intelligence platforms use machine learning algorithms to analyze network traffic, identify anomalies, and detect potential security breaches in real-time.
This proactive approach allows security teams to respond swiftly to emerging threats, minimizing the potential impact on operations. For instance, a power generation company implementing continuous threat monitoring was able to detect and neutralize a sophisticated phishing attack before it could compromise their control systems, potentially saving millions in damages and downtime.
Employee cybersecurity training programs strengthening resilience
While technological solutions are crucial, the human element remains a critical factor in cybersecurity. Comprehensive employee training programs are essential in creating a culture of security awareness within an organization. These programs should cover topics such as:
- Recognizing and reporting phishing attempts
- Proper handling of sensitive data
- Understanding and adhering to security policies
- Best practices for password management and device security
- Procedures for responding to potential security incidents
By empowering employees with knowledge and skills to identify and respond to cyber threats, industries can significantly enhance their overall security posture and reduce the risk of human-error-related incidents.
Tailoring solutions to Industry-Specific challenges requirements
While many industrial optimization strategies are broadly applicable, the most effective solutions are those tailored to address the unique challenges and requirements of specific industries. This customized approach ensures that technologies and processes are aligned with the particular needs of each sector, maximizing their impact and return on investment.
Modular customizable platforms adapting to unique needs
The development of modular, customizable platforms has revolutionized the way industries approach technology integration. These flexible systems allow companies to select and combine different modules based on their specific requirements, creating a tailored solution that addresses their unique challenges.
For example, a pharmaceutical company might prioritize modules focused on precision control and regulatory compliance, while a logistics firm might emphasize real-time tracking and route optimization. This modular approach not only provides a more targeted solution but also allows for easier upgrades and expansions as needs evolve.
Close collaboration between vendors clients ensuring fit
The most successful industrial solutions are often the result of close collaboration between technology vendors and their clients. This partnership approach ensures that the implemented solutions are not only technically sound but also align perfectly with the client’s operational processes and business objectives.
Through workshops, site visits, and ongoing consultations, vendors can gain a deep understanding of their clients’ needs and challenges. This insight allows them to develop and refine solutions that address specific pain points and deliver tangible value. For instance, a digital workspace solution provider working closely with a manufacturing client was able to create a custom interface that streamlined communication between shop floor workers and management, significantly improving operational efficiency.
Iterative agile development methodologies delivering results
In the fast-paced world of industrial technology, the ability to adapt quickly to changing requirements is crucial. Adopting agile development methodologies allows for an iterative approach to solution implementation, where feedback and results from each phase inform the next steps.
This approach enables companies to see tangible results faster and make necessary adjustments along the way. For example, a chemical processing plant implementing a new control system using agile methodologies was able to achieve a 20% improvement in process efficiency within the first three months, with further enhancements rolled out in subsequent iterations.
Leveraging cloud computing for scalable flexible deployments
Cloud computing has emerged as a game-changer in industrial optimization, offering unprecedented scalability, flexibility, and cost-efficiency. By moving key applications and data to the cloud, industries can access powerful computing resources on-demand, without the need for significant upfront investments in hardware and infrastructure.
The benefits of cloud-based solutions in industrial settings are numerous:
- Rapid deployment and scaling of applications
- Enhanced collaboration and data sharing across locations
- Improved disaster recovery and business continuity
- Access to advanced analytics and AI capabilities
- Reduced IT maintenance and management costs
For instance, a global manufacturing company leveraging cloud-based analytics was able to consolidate data from multiple facilities, gaining insights that led to a 15% reduction in overall energy consumption across their operations. The scalability of cloud solutions also allows companies to easily expand their capabilities as their needs grow, without the limitations of physical infrastructure.
As industries continue to evolve and face new challenges, the integration of smart, secure, and tailored solutions will remain crucial for maintaining competitiveness and driving innovation. By embracing these technologies and approaches, companies can not only optimize their current operations but also position themselves for future growth and success in an increasingly digital industrial landscape.